Solutions
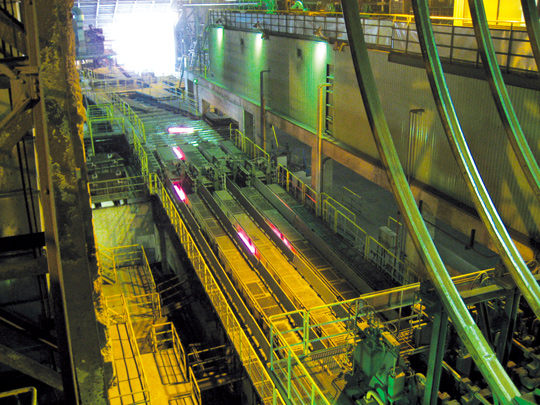
-
6.0 m/min
high-speed casting
Production Cost Reduction / Production Volume Increase
Adoption of Steel Plantech’s continuous casting facilities makes it possible to reduce production costs.
- 1Energy-saving through sequentialized processes enabled by direct coupling to rolling machines.
- 2Power-saving through automated and serialized operational procedures, and equipment monitoring system.
- 3Realization of productivity enhancement through improved capacity utilization and high-speed casting.
- 4Ensured maintainability through easy access to major equipment segments and use of maintenance equipment and failure diagnosis system.
- 5Stable casting and reduction of unstable parts through mold-level control and optimum secondary cooling capabilities.
- 6Reduction of energy and costs required for rolling through near net shape casting (slabs close in shape to the final product).
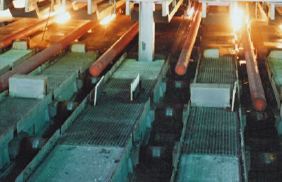
Product Range Expansion
Steel Plantech has abundant experience in the development of multifunctional machines for a wide variety of slab sizes and steel grades.
- 1Billet (vertical, horizontal and circular machines for square, round, octagon and other shapes)
- 2Bloom size (not only small to large sizes but round also possible)
- 3Beam blank (maximum size of manufacture: 450×1,048x110mm)
- 4Dual-use slab/billet and bloom casters
- 5Blast furnace ordinary steel, electric arc furnace ordinary steel, special steel, stainless steel
- 6Learning-type break-out (BO) prediction device that prevents breakouts
- 7Dynamic secondary cooling system and dynamic soft reduction system